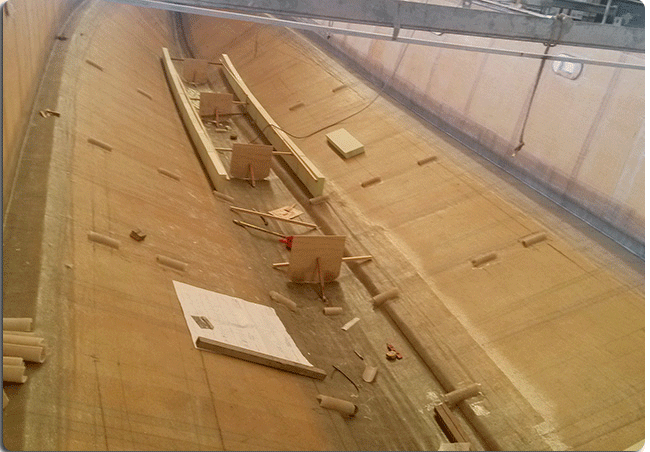
The inner fiberglass laminate for the Hunt 80 has been applied over the foam core, completing the continuous structural I-beam created by the core and inner and other hull skins. Note the solid laminate overlaps at the chines, adding extra strength and compression resistance to handle the loads induced by lifting straps. Coring creates a very stiff and strong structure while reducing weight substantially compared to a solid fiberglass hull. The first two stringer sections are seen in place forward to port and starboard of the keel.
More stringers are being laid and then bonded in place for follow-on lamination. The stringers, which run longitudinally for most of the length of the hull, are made of structural foam encapsulated in fiberglass laminates. Stringers stiffen and strengthen the hull bottom, while serving as a foundation for the decks and machinery to follow. Once the bulkheads are installed, the bottom of the hull will essentially be divided into many small panels defined by the spacing of the interlocking network of stringers and bulkheads. The whole structure is meticulously engineered to optimize strength while minimizing weight, and this process includes precise alignment of the components with the help of the transit seen here atop the keel section.
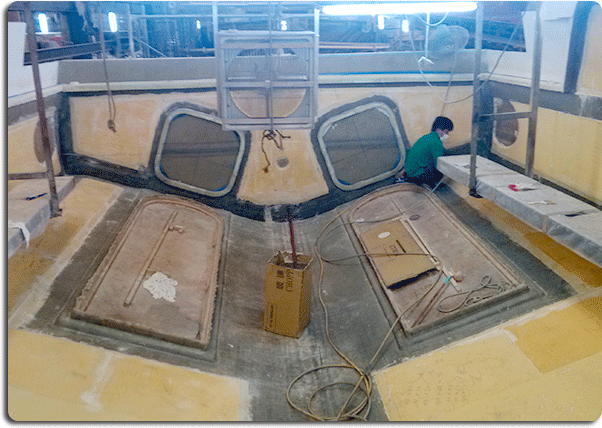
Templates are used to precisely position and outline the waterjet intakes in the bottom of the hull, as well as the nozzles in the transom. When the lamination process is complete, holes will be cut in the hull bottom and transom to precisely match the waterjet machinery. The hull immediately adjacent to the intakes is solid fiberglass so that the mounting bolts have a non-compressible surface to attach to, and to absorb vibrations effectively. The edges of the coring are tapered to provide a smooth transition for the inner fiberglass laminate from the surrounding core to solid glass.